ERFOLGREICH CASE
Projektstandort: Deutschland
Projektlaufzeit: 2012
Kunden die wichtigsten Produkte: Endgültige Batch - Kautschuk (für Gummidichtungen), einer der größten Rohrdichtungshersteller in Europa
XINDA Maschine: 3-Flug Co-Kneter SJW-200
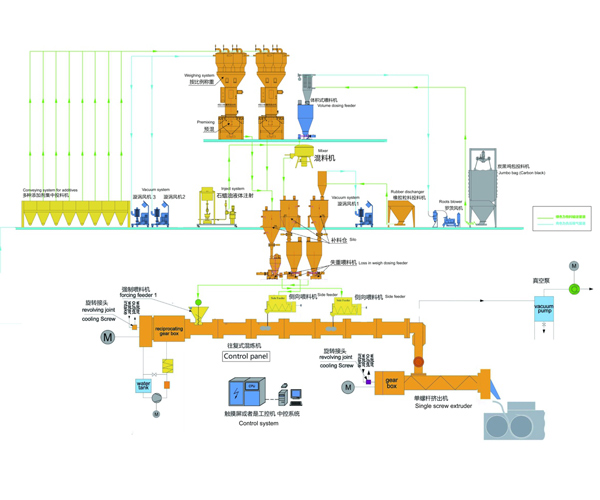
Einführung des Projekts
1. Im Jahr 2011 hat der Kunde den neuen Produktionsprozess ihrer Produkte mit XINDA besprochen, und beide Parteien bestimmen in R & D. Während dieser Zeit zusammenarbeiten, bereinigt sie den Produktionsprozess in Xinda Labor für viele Male und nahm es zurück nach Deutschland für wiederholte Tests. Die endgültige Produktqualität überschritt das Original.
2.In 2012, the customer purchased xinda co-kneader SJW-200 to produce final batch rubber for rubber seal products, changing the processing technology of traditional banbury kneaders and milling rollers, which greatly improved the stability of product performance. At the same time, high degree of automation of Co-kneader improved the workshop production environment. The capacity per unit compounding line can reach 10,000 tons/year.
Kunden Feedback und Bewertung
1. Niedrige Scherung und hohe Dispersion ist das einzigartige Merkmal der Co-Kneter. Rohstoffe, wie Gummipartikel, Ruß, Weißöl, Gummi Beschleunigers und des Härtungsmittels und so weiter, geben wiederum auf der Hubkolbenmaschine abschnittsweise mit genauen Materialtemperatursteuerung, eine ausreichende Dispersion und Mischen, ausgezeichnete Produktleistung und gute Produkthomogenität und Stabilität.
2. Automatisierungsgrad von Co-Kneter in der Produktion ist extrem hoch. Rohstoffe können in Gruppen auf und dosiert in Abschnitte durch die gravimetrische Beschickungssystem unterteilt werden. Die Kautschukteilchen, Ruß, Weißöl und Vulkanisationsmittel werden in einer geschlossenen Art und Weise zugeführt. So ist die Werkstatt Produktionsumgebung ist sehr sauber.
3.Three-flight Co-Kneter SJW-200 hat eine hohe Produktionskapazität und geringen Energieverbrauch. Verglichen mit der traditionellen internen Veredelung plus offen Raffinierung Produktionsanlagen, wird der Energieverbrauch pro Tonne um 20% reduziert - 30%.
4. Die obere Stufe hin- und hergehenden Maschine nimmt eine Clamshell Faßentwurf, während Schraube der zweiten Stufe Extruder pelletisiert kann durch Zurückziehen getrennt werden. Wenn daher Formeln oder die Maschine muss gewartet ändern, kann es schnell geöffnet und gereinigt werden, was die Zeit der Umkehr und die Wartung verkürzt.
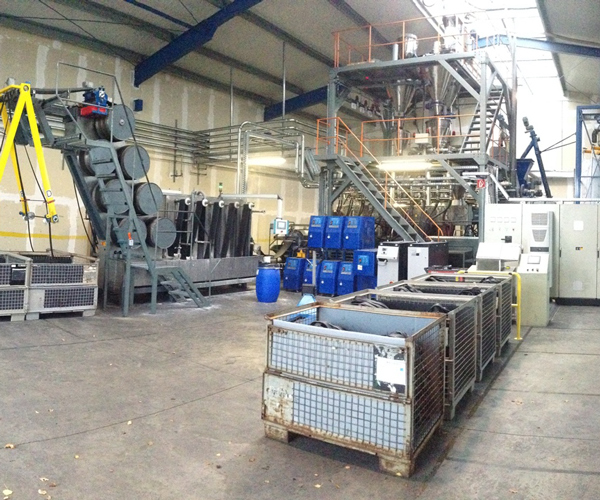
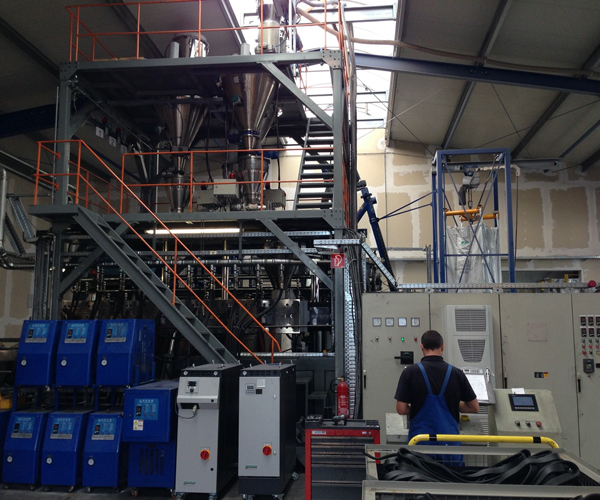