There are two-step method and one-step method for the production of silane cross-linked cable material and its cables. It is believed that the difference between the two-step method and the one-step method is where the silane grafting process takes place. The two-step method is used for the grafting process at the cable material manufacturer, and the one-step method is used for the grafting process at the cable manufacturing plant.
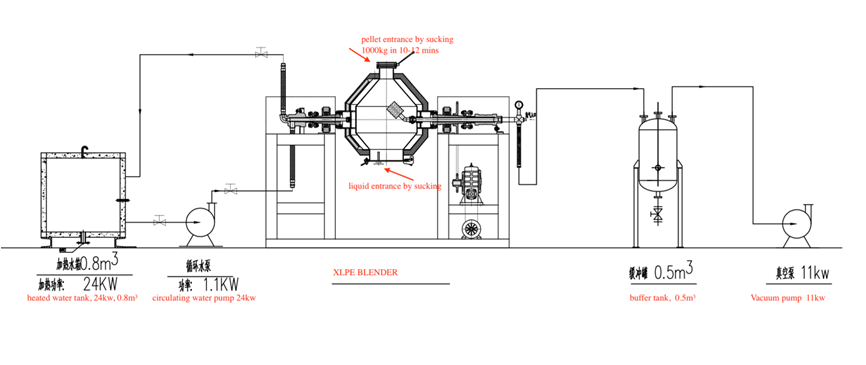
At present, the two-step silane crosslinked polyethylene insulation material with the largest domestic market share is composed of material A and material B. Material A is polyethylene which has been grafted with silane, and material B is a catalyst masterbatch. Its weight ratio is generally A : B = 95: 5. Materials A and B are made by the cable material factory and then sold to the cable factory. Before the cable factory mixes the materials A and B in proportion, the cable can be extruded on the ordinary extruder.
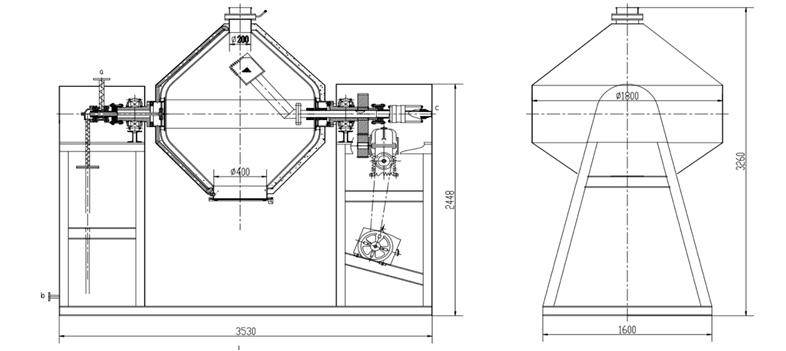
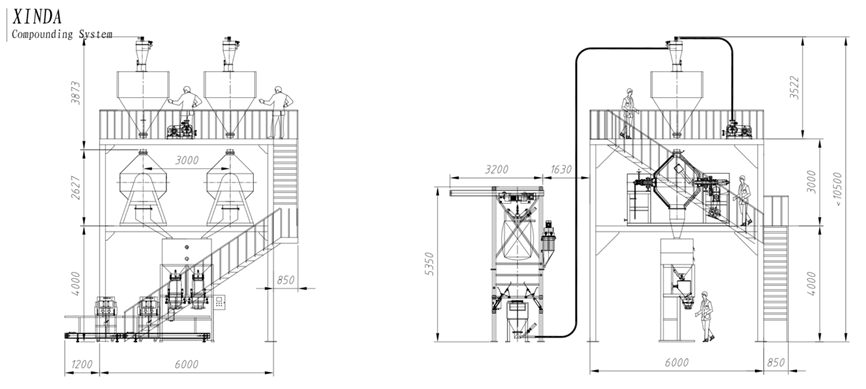
There is also a type of two-step silane cross-linked polyethylene insulation material. The production method of material A is different. In the process of synthesizing polyethylene, vinyl silane is directly introduced to produce polyethylene containing silane branches. This method is essentially a resin production technology that must be completed by a large petrochemical company. The first material of LINKLON silane material that entered the Chinese market belongs to this type. Currently, DOW and BOREALIS silane materials are also of this type.
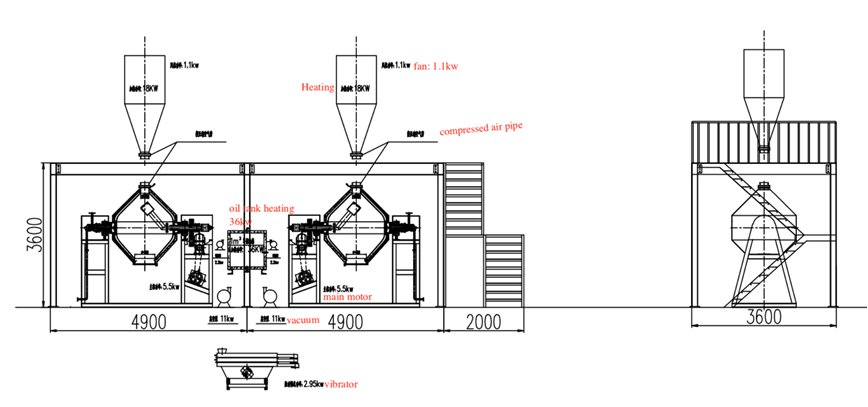
One-step silane cross-linked polyethylene insulation can also be divided into two types. The traditional one-step process is to put various raw materials into a specially designed extruder in a specially designed extruder to complete the grafting and extruding of the cable in one step. In this process, there is no need for granulation, nor the participation of the cable material factory, which is completed by the cable factory alone. Another type of one-step silane cross-linked polyethylene insulation material is produced by cable material manufacturers. All raw materials are mixed together in a special method according to the formula in the formula, packaged and sold, and there is no material A and B. The cable factory can directly graft and extrude the cable in one step in the ordinary PVC extruder. Its characteristics are: the composition of the base material is 40 to 85 parts of low density polyethylene (LDPE) and 15 to 60 parts of linear low density polyethylene (LLDPE); the composition of the masterbatch of the catalyst is: low density polyethylene (LDPE) is one 100 parts of a mixture of one or more types of polyethylene, 1 to 10 parts of antioxidants, 1 to 10 parts of copper inhibitors, and 1 to 10 parts of catalyst; the composition of silane crosslinking compounding agent is: 100 parts of silane and 10 to initiator 50 parts, mix well. Compared with the traditional two-step method, the effect and benefit of the present invention is that there is no A and B materials, and all raw materials are mixed together in a special method according to the ratio, and the cable factory can directly complete it in one step in the extruder. Grafting and extruding cable insulation cores can be completed in an ordinary extruder, and the labor of mixing the A and B materials before extrusion in the two-step process is eliminated, the process is simple, the equipment investment is small, and the product performance is stable. Long storage period.
